Success Story: Gettysburg Flag Works Optimizes Space, Saves Big with CEG BGS’ Help
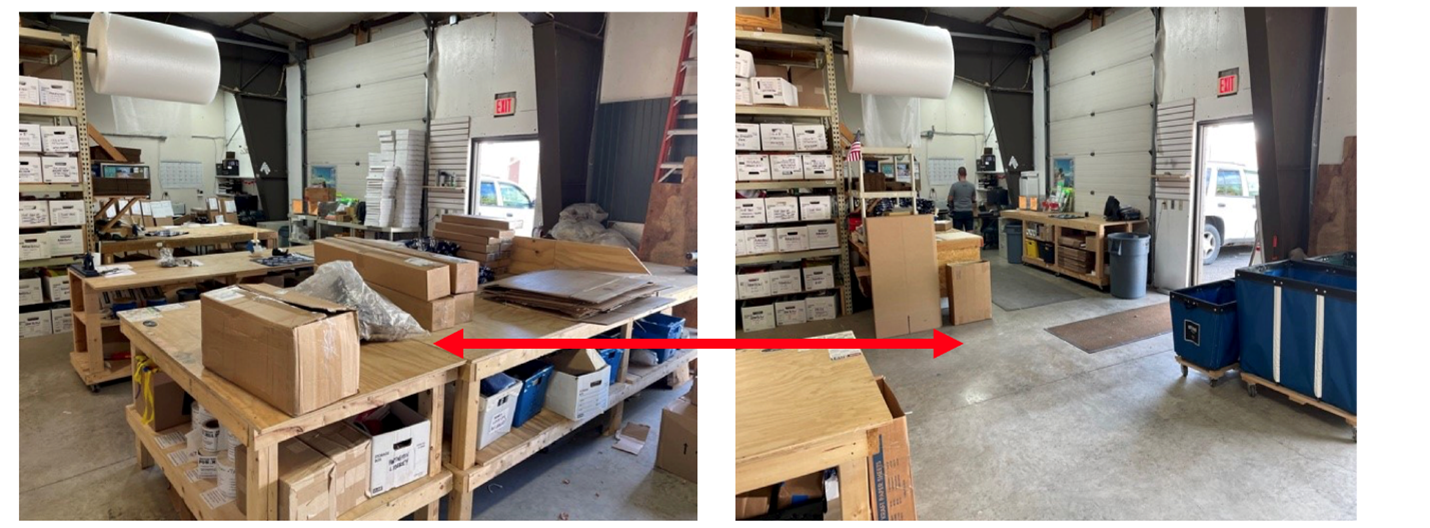
Before and after pictures showing optimized floor utilization at Gettysburg Flag Work’s East Greenbush facility.
Overview
Gettysburg Flag Works manufactures custom flags and banners. Founded by an Army veteran, Mike Cronin, in 1993, the manufacturer has been operating out of a 6,000-square-foot building in East Greenbush since 2006. Gettysburg Flag regularly maintains an inventory of 250,000 units, including flags, banners, flagpoles, clips and rope. The company employs 20 workers.
The Situation
During the pandemic, Gettysburg Flag saw a stronger demand for its products that quickly tested the spatial capacity of its facility, especially its 2,000 square feet of warehouse space. The building also houses Gettysburg Flag’s retail store. “We realized we had some growing pains early in the pandemic,” said Gettysburg Flag President Andrew Kinerson.
In 2021, Gettysburg Flag’s co-owners inquired about expanding their building to allocate more space to manufacturing for both storage of goods. Their manufacturing process also needed more space because of both growth and reaction to supply chain issues. That was when Gettysburg Flag’s lender recommended the company connect with the Center for Economic Growth’s Business Growth Solutions (CEG BGS) unit, which is part of New York’s Manufacturing Extension Partnership.
The Situation
Following meetings with Gettysburg Flag to understand their needs and current situation, CEG BGS engaged with strategic partner, Larry Treen of Relay Integrated Logistics & Solutions. The goal of this project was to assist Gettysburg Flag in optimizing what space was already available to it within the current footprint. With Treen, Gettysburg Flag looked to improve the areas of picking and packing, vendor drop-ship techniques. They also sought to optimize cash flow and turning of inventory.
Treen mapped a future state layout to fully optimize the space that Gettysburg Flag already had, eliminating the need to blow out a wall and pursue a full-on construction project. Treen also looked at inventory, floor layout, and particularly the pack-and-ship station layout to ensure maximum productivity and best-case utilization of space. Kinerson said he gained about 850 square feet of space by looking at the storage space more as a three-dimensional cube and taking advantage of more compact vertical shelving.
“Not only did he give us more space, [Larry] optimized how we use it,” Kinerson said.
Results
This project helped Gettysburg Flag avoid $250,000 in expansion-related costs.
Testimonial
“We had thought about optimizing the building rather than expanding, but we weren’t sure we could get it to where we needed it. The Center for Economic Growth’s Business Growth Solutions and Relay Integrated Logistics & Solutions gave us an outside perspective that proved we can. Now we can accommodate more staff, more inventory, and we should be able to continue operating out of our building for an additional three to five years.”
Gettysburg Flag Works, President, Andrew Kinerson